A legtöbb ember annyit tud a csavarozásról és a hasonló rögzítési megoldásokról, hogy csavarhúzó kell hozzá, ami többségünknek legfeljebb egy-egy új bútor összeszerelésekor, vagy valami régi, szétesőfélben lévő tárgy szerelésekor kerül elő. A különféle gyártó és összeszerelő üzemekben azonban ennél sokkal komolyabban kell venni a kötéstechnika világának műveleteit, hiszen ezen áll vagy bukik, hogy egy termék tartós, minőségi darab vagy szemétre való bóvli lesz. Ebbe a hétköznapi emberek által ritkán látható világba Medveczky Zoltán, a Bosch Rexroth Kft. terméktámogató mérnöke vezetett be minket.
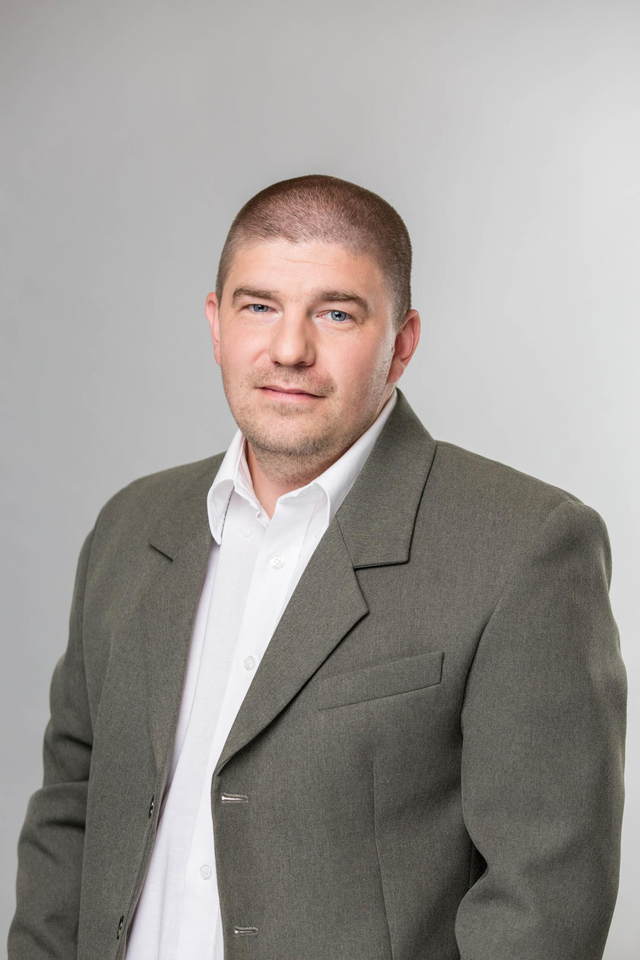
Medveczky Zoltán, a Bosch Rexroth Kft. terméktámogató mérnöke
Bosch Rexroth Kft.
„A különféle termékek gyártása során végbemenő csavarozási, hegesztési folyamatok kifejezetten termékspecifikusak, hiszen teljesen máshogyan kell összeszerelni egy háztartási gépet és egy autót” – mutatott rá Medveczky Zoltán. „A hasonló szegmensben dolgozó gyártóknál lehetnek azért hasonló megoldások, azaz két autógyártónál a motor vagy a karosszéria gyártása nagyjából azonos folyamatokból áll, kisebb-nagyobb eltérésekkel. Ami viszont megegyezik, azok az úgynevezett folyamatközi ellenőrzések. Bármilyen terméket gyártsunk is, a minőség biztosítása miatt vannak olyan pontok, ahol különféle vizsgálatokra kerül sor.”
A különféle iparágakban természetesen megvan az adott szektorra, szegmensre jellemző belső szabályozás, amit mindenkinek be kell tartania, emellett minden gyártónak megvannak a saját „házi praktikái”, amikkel megpróbálják kiküszöbölni a gyártási hibákat. Medveczky Zoltán rámutatott, hogy a csavarozás-, illetve hegesztéstechnikai műveletek jelentős részét az autóiparban végzik, ugyanis a motortól kezdve az egész jármű összeszereléséig rengeteg csavarra van szükség, míg a karosszéria összeillesztésénél a hegesztési folyamatoké a főszerep.
„Utóbbi szűkebb terület, de a csavarozási technológiákat szélesebb körben is alkalmazzák” – hangsúlyozta a szakember. „Magyarországon is rengeteg olyan vállalat és gyártóüzem működik, ahol valamit összeszerelnek, a csavarkötés pedig az egyik legelterjedtebb kötési technológia, így a Bosch Rexroth termékeit sok helyen használják.”
A csavarozásnak különböző fokozatai vannak, ezek közül a legegyszerűbb a kézi megoldás, ezt mindenki ismeri: fogunk egy csavarhúzót – szaknyelven kézi csavarbehajtót –, és behajtjuk a szükséges csavart. Ennél azonban vannak nagyobb figyelmet igénylő műveletek is. A Bosch Rexroth szakértője rámutatott, hogy három fő kategóriába lehet sorolni a csavarozási folyamatokat. Az úgynevezett A-típusú csavarkötések olyanok, amelyeknek a hibája akár az emberi életet is veszélyeztetheti. Ilyen például egy autó fék- vagy kormányrendszere, ahol egyetlen hibás csavar is tragédiához vezethet.
„Ez a technológia csúcsa, ahol komoly adatmentésre is szükség van, mert a gyárnak tudnia kell igazolni, hogy a folyamat rendben lezajlott” – magyarázta Medveczky Zoltán. „Ilyenkor fixálni kell a nyomatékot és a szögelfordulást, de akár egy grafikonon a szög- és nyomatékgörbét is, illetve rögzíteni kell, hogy hogyan történt meg a lefuttatás, és ez hogyan felelt meg a megadott specifikációnak.”
A B-kategóriába olyan termékek és műveletek tartoznak, ahol a csavarkötés legfeljebb a funkció szempontjából kritikus, vagyis ahol az adott termék vagy eszköz nem működik, ha nem megfelelő a kötés.
Minden más pedig a C-kategóriába tartozik: ezek a legegyszerűbb csavarozások, amelyekről nem is szükséges adatokat menteni, csupán be kell hajtani a csavarokat a megfelelő helyre.
„A Bosch Rexrothnál mi az A- és a B-kategóriákhoz gyártunk és forgalmazunk termékeket” – tette hozzá Medveczky. „Mivel azonban a Bosch csoport tagja vagyunk, a C kategóriás esetekben a Robert Bosch Power Tools kéziszerszámokkal szoktuk kiegészíteni a szolgáltatást, hogy teljes lefedettséget tudjunk biztosítani.”
A szakembertől megtudtuk, hogy a komplex késztermékek gyártása során precíz lépéseket követve részegységekre bontják a nagy egészet, ügyelve rá, hogy az egyes munkafázisok ne „üssék” egymást, azaz egy korábban elvégzett művelet nem akadályozhat egy későbbi lépést.
„A legfontosabb, hogy a munkafolyamatokat úgy állítsuk össze, hogy egyik részleg se tartsa fel a másikat, ne álljon a gyártósor” – hangsúlyozta Medveczky Zoltán. „Ilyenkor kritikus feladat az úgynevezett ciklusidők tervezése, hogy egyik gépsor se álljon túl sokáig. Ha pedig szükséges, akkor további részlépésekre kell bontani az egyes fázisokat. Erre azért van szükség, mert egy motor összeszerelésénél 2-300 csavarozási műveletet is végre kell hajtani, ebből adódóan pedig nagyon meg kell tervezni, hogy melyik állomáson, hány csavarozóval, hány folyamatot végzünk el egyszerre. Ez még papíron történik meg, a tervezés során, és ezután, ha felépült a gyártósor, utólag lehet paraméterezéssel finomítani tovább.”
A fizikai munka mellett a Bosch Rexroth által is fejlesztett ipari eszközök és szoftverek is kiveszik a részüket a digitális nyilvántartásból. Maguk a gyártóberendezések ugyanis képesek elvégezni az elsődleges ellenőrzéseket, legyen szó akár egy szerszámgépről, egy csavarozási, hegesztési vagy préselési folyamatról.
„Ilyenkor maga a berendezés képes mérni, amit éppen csinál, és tartani az előre beállított határértékeket” – mondta a szakember. „Ezen felül azonban minden gyártósorba be vannak építve úgynevezett ellenőrző kapuk. Például bármilyen vezérlőelektronika gyártásakor az alkatrészek beültetése után azonnal megtörténik a vizuális ellenőrzés, a forrasztások után pedig áramköri teszteket végeznek a kollégák, hogy minden alkatrész a helyére került-e. Amikor pedig már minden a helyén van, funkcióteszt következik, hogy az összeszerelt termék valóban képes-e ellátni azokat a funkciókat, amelyeket az ügyfél elvár. A végén pedig több optikai vizsgálat során kamerákkal is megvizsgálják a paneleket, hogy minden a helyére került-e, de a címkét is megnézik, hogy helyes pozícióba került-e, a szükséges szöveggel együtt. Természetesen később szúrópróbaszerűen is ellenőrzik a termékeket, azaz bizonyos darabszám után egyet-egyet kivesznek a gyártósorról, és teljes részletességgel megvizsgálják.”
A sok biztonsági „szelep” ellenére előfordulhat, hogy mégis hibás termék érkezik a gyártósorról. Ilyenkor különböző folyamatok indulnak be, attól függően, hogy milyen elégtelenséget tártak fel. Ez két nagy csoportra osztható: egyfelől olyan termékhibákra, amelyek egy hibás folyamatra vezethetők vissza, azaz valamelyik lépést nem jól végezték el. A másik kategóriába pedig azok az esetek tartoznak, amikor valamilyen módon maga a gyártóberendezés hibásodik meg.
„Jó esetben ez utóbbi kevésbé kritikus, mert egyrészt ezt gyakran a gép maga jelzi, másrészt pedig ilyenkor legalább nem jön létre hibás, selejtes termék” – mutatott rá Medveczky Zoltán. „Ez ellen nehéz védekezni, mert előfordulhat áramköri túlterhelés, villámcsapás, anyagfáradás és hasonlók – ezek ellen részben a rendszeres karbantartással lehet védekezni. A másik eset, amikor a technológiából adódóan jelentkezik valamilyen hiba a gyártás során. A gyártásban szerzett tapasztalataim alapján mondhatom, hogy ilyenkor beindul a cég teljes minőségbiztosítási gépezete, ami egy mindennél alaposabb ellenőrzést jelent, hogy megállapítsák, pontosan mi a hiba oka, a hiba előfordult-e már korábban, vagy esetleg valamelyik ellenőrző ponton csúszott át. Ezt követően vagy szigorítást vezetnek be az adott ponton (esetleg az ellenőrző pontokat kezdik finomítani), vagy a gépek szoftverének a programján változtatnak. Természetesen ilyenkor komoly dokumentáció is készül, illetve történik egy elsődleges, rövidtávú hibaelhárítás, majd ezután jön az az átépítés, átalakítás, amely elejét veszi egy hasonló hiba újbóli bekövetkezésének.”
A termeléssel foglalkozó vállalatok már több mint egy évtizede építenek komplex adatbázisokat a különféle gépek és folyamatok technikai részleteiről. Ezeket ma már a fejlett szoftveres háttérnek és a mesterséges intelligenciának köszönhetően rendkívül gyorsan, akár valós időben is lehet elemezni, ráadásul a gépi agy olyan összefüggéseket, mintákat is észre tud venni, amelyeket egy ember nem, vagy legfeljebb nagyon lassan találna meg.
„A mesterséges intelligencia használata sokat segít a megelőző karbantartások tervezésénél, mert olyan adatokat is képes figyelni, hogy milyen tartományban működik például egy csavarozó” – tette hozzá Medveczky Zoltán. „Előfordulhat, hogy idővel elkezd eltolódni az előre beállított érték, de az így készülő termék még átmegy az ellenőrzéseken. A mesterséges intelligencia viszont már ezen a ponton tud jelezni, így elejét lehet venni annak, hogy valamelyik mechanikus komponens meghibásodása miatt a komplett gyártósornak hirtelen le kelljen állnia.”
A szakember szerint a modern, digitalizált gyártóüzemekben olyan szakemberekre is szükség van, akik a konkrét gyártás mellett az informatikai háttér működésében is otthonosan mozognak. Kellenek az ilyen üzemekbe adatbányászok és adatfeldolgozásban jártas szakértők, de a folyamatmérnököknek is tudniuk kell, hogy melyik géppel mi történik éppen. Ugyanígy az operátoroknak is résen kell lenniük, hiszen nekik a különböző gépek működése során kell kiszúrniuk az apróbb rendellenességeket.
„Itt minden szereplőnek fontos része van az olajozott működésben” – mondta a szakember. „Az adatbányászat most sok helyen megjelent, mert rengeteg időt lehet vele megspórolni, de továbbra is szükség lesz villamosmérnökökre, gépészekre, operátorokra, még úgy is, hogy már sok helyen használunk robotokat az egyszerűbb feladatok elvégzésére – például a mi kínálatunkban is elérhető Kassow robotot, amely alkalmas rá, hogy emberekkel egy légtérben dolgozzon kollaboratív robotként.”
Az olajozott gépezetként működő gyártás pedig kulcsfontosságú, mivel napjainkban, a gazdasági és energiaválság közepén senki sem engedheti meg magának a pazarlást. Ezért került minden cégvezető fókuszába az elmúlt időben a hatékonyság, amely egyaránt kiterjed a termelékenységre, de a működési költségekre – így például az energiaszámlára –is.
„A Bosch Rexroth-nál már hosszú évek óta figyelünk rá, hogy az újabb technológiák minél energiahatékonyabban működjenek” – jegyezte meg Medveczky Zoltán. „A hidraulikus rendszereinknél kezdtük el a fenntarthatóbb működés kialakítását, aztán jöttek a tápegységek, illetve az úgynevezett fordulatszám-szabályozott rendszerek, amelyek csak akkor adnak le teljesítményt, ha szükség van rá, a köztes időben pedig nem fogyasztják az energiát. Ugyanez igaz a legújabb csavarozó rendszereinkre, ahol az eszközök hűtése és egyéb működése is ehhez hasonlóan van konfigurálva. Olyan szolgáltatást is nyújtunk, amelynek keretében felmérjük egy régi berendezés aktuális energiahasználatát, és kiszámoljuk, hogy mennyit lehetne megtakarítani, ha a mi eszközeink segítségével modernizálnák. Emellett része a portfóliónknak a régi gépek modernizálása is, hiszen egy jól működő, régi eszközt nem biztos, hogy megéri lecserélni, ha költséghatékonyan bekapcsolható az Ipar 4.0-s működésbe.”
NEXO: több mint tíz éve az ipar szolgálatában
NEXO: több mint tíz éve az ipar szolgálatában A Bosch Rexroth szakemberei nemrég mutatták be a piacnak a NEXO csavarozó berendezésük második generációs változatát, amely egy vezeték nélküli, akkumulátoros, wifi-modullal ellátott ipari csavarozó berendezés, kifejezetten olyan helyekre kifejlesztve, ahol az eszközből kilógó kábel zavaró lenne. A második generációs NEXO csavarozóba integrálták a vezérlést és a wifi-kommunikációt is, az eszköz külső vezérlőegység nélkül képes kommunikálni a fölérendelt vezérlő berendezésekkel, adatbázisokkal. Beépített kamerájával bármilyen ipari kódot, QR-, vagy vonalkódot be tud olvasni, így lehet vele azonosítani egy-egy adott terméket, de akár egyetlen kattintással ki lehet választani az adott munkafázishoz szükséges csavarozási programot is. A Bosch Rexroth megoldása kihasználja a szinergiát a Robert Bosch Power Tools kéziszerszámaival is, hiszen ugyanazt az akkumulátort használja, de a Bosch Rexroth szakemberei az anyacég kézi csavarozás-technológiáját is alkalmazzák csavarozástechnikai megoldásaikban. | A tartalom a Bosch Rexroth Kft. megbízásából, a HVG BrandLab produkciójában készült. A cikk létrehozásában a HVG hetilap és a hvg.hu szerkesztősége nem vett részt.
A tartalom a Bosch Rexroth Kft. megbízásából, a HVG BrandLab produkciójában készült. A cikk létrehozásában a HVG hetilap és a hvg.hu szerkesztősége nem vett részt.